Things Hansen Pole Buildings Does Better Than Any Other Post-Frame Building Provider
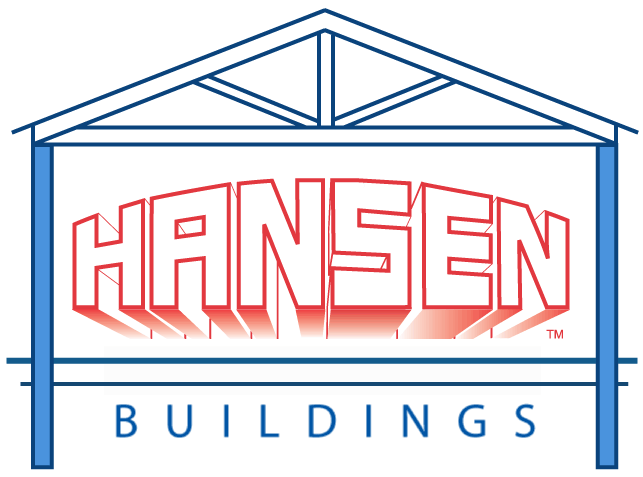
To those of you who have read my previous 13 articles, this will serve as a recap. For you who have not, please peruse when you have an opportunity.
STRONGEST GLULAM COLUMNS
While manufactured from lumber 157% as strong as what is typically found, they have many other benefits. These include (on pressure treated applications) every lamination being completely saturated with preservative chemicals for in-ground portion and roughly 1/3rd weight of a solid sawn 6×6. Glu-lam columns tend to be highly resistant to warp and twist.
SAVINGS FOR BRACKET MOUNTED APPLICATIONS
For bracket mounted application, our same ultra high strength glu-lams are available untreated, helping offset costs of our ICC-ESR code compliant wet set brackets.
COLUMNS NEXT TO DOOR OPENINGS
Not every provider places columns next to every door opening. Not for your doors – either a glu-lam or a bracket mounted kiln dried Douglas Fir timber will support both sides of every door opening!
FOUNDATION RATED #1 GRADE SPLASH PLANKS
Fewer defects, pressure treated throughout and kiln dried after treating for lighter weight.
LUMBER-TO-LUMBER CONNECTIONS
Simpson SDSW16300 screws afford greater strengths and easier adjustments than any sort of nailed connection.
DOUGLAS-FIR WALL GIRT LUMBER
Douglas-Fir is greatly prized for strength and dimensional stability. Less prone to warp, cup, bow and twist than other framing lumber species. 2X8 and 2×10 bookshelf wall girts are PREMIUM graded, minimizing wane (and possible screw misses).
HIGHER GRADED TRUSS LUMBER
No Utility, Standard, Stud or #3 lumber in Hansen Pole Buildings’ trusses. All material is no less than #2 grade.
EASY INSTALL PURLIN HANGERS
Simpson PFDS series hangers slide over pairs of roof trusses and screw to top chords, making for a quick install of hangers as well as connecting chords together at same time.
END PAINTED FRAMING MEMBERS
Wall girts, roof purlins, floor and ceiling joists all have one end uniquely color painted. This immediately allows DIY clients, building erectors and inspectors to quickly identify correct placement of these materials.
EASILY MEASURED SPACING OF WALL GIRTS AND ROOF PURLINS
Spacing has been standardized to fall so measures are evenly divisible into eight (8) feet. Examples are 32”, 24”, 19.2” and 16”, all of these are keyed to markings on standard tape measures. This also matches with applications of 4’ x 8’ sheet goods (plywood, OSB, etc.).
RAISED HEEL INTERIOR TRUSSES
When endwall overhangs are ordered in conjunction with ceiling joists, interior truss heels are greater (raised) in order to have all truss bottoms at same height above grade.
HIGH GRADE RAFTERS
For rafter applications (side or end sheds, monitor building wings) Hansen Pole Buildings has invested in MSR (Machine Stress Rated) lumber 243 to 266% stronger than #2 grades of Douglas-Fir (even greater in comparison to Southern Pine). This allows for greater spans and fewer pieces needing to be used.
FABULOUS FLOOR TRUSSES
By utilizing higher strength lumber, your second floor can be clear-spanned with roughly one inch of truss depth per 18 inches of truss span. Eliminate a profusion of interior columns and bearing walls, HVAC and plumbing can be run through, creating a flat finished ceiling.
MILL DIRECT BUYING
We have cut out middleman wholesalers and retailers buy going direct to mills for multiple truck and rail car loads of lumber – passing these savings on to you!
SHARED TRUCKING
Our shipping expediters consolidate buildings being shipped geographically to minimize freight investments for our clients.
EXTRA SAVINGS FOR STANDARD DIMENSIONS
As lumber comes in two foot lengths and steel roofing and siding in three foot widths, there is already savings to be found in multiples of six feet (less waste). Choose a width in six foot multiples (12’, 18’, 24’, 30’, etc.) and a length of a 12 foot multiple and receive an extra 5% discount!
THE ULTIMATE POST FRAME BUILDING EXPERIENCE
No one does post frame better than Hansen Pole Buildings – and if you are not yet convinced, watch subsequent articles for even more benefits for you!
Don’t rely upon a builder to look out for your best interests in materials’ selection – take control by ordering from us and pay an erector to assemble,