My good friend John owns (among other things) Heartland Permacolumn. I’ve borrowed this from his website (https://www.heartlandpermacolumn.com/products/the-perma-column-price-advantage/):
“Perma-Column products give you the ultimate price advantage. You simply cannot put up a building on a concrete foundation for less money.
Yet some may say, “They’re too expensive…”
HOWEVER, the only people who ever say this install buildings using treated wood posts embedded directly in the soil. They think adding between one and three thousand dollars to a building makes the price “outta sight…”
It is true that there is one type of building that is less expensive than a Perma-Column building…one built on a treated wood foundation. Treated wood posts may last a very long time in soil contact in some cases…and not so long in other cases. This is part of what makes post-frame buildings the most economical of all building types.
But there are several other reasons why post-frame is so economical and efficient. First, it is much quicker, easier and less resource-intensive to stick a post in the ground and build from there than it is to build any other type of building on a typical foundation.
Second, by using posts that are 8′ or more on center, you have far fewer structural members to install compared to other types of buildings.
Third, because the structure is made of wood it is less costly, requires no fancy equipment or specialty trades, is easier to work with, is very environmentally-friendly and is energy-efficient.
Furthermore you can build exceptionally high sidewalls (usually 24′, sometimes more) and exceptionally wide clear-spans (100′ or more without supporting walls or columns) for ultimate design efficiency and flexibiliity. All of these advantages remain firmly in place when you build on concrete piers or a continuous concrete foundation using Perma-Column products.
When one takes a close look at costs per linear foot, the upgrade is not really very much at all. A Perma-Column upgrade is typically between $10 and $11 per linear foot compared to the price of building on treated wood posts embedded directly in the ground. This may increase the price of a really small and inexpensive agricultural building by more than 10%, but it may also add less than 4% to the total cost of a really nice one…or to a typical commercial, residential or industrial building. Click here to download a PDF that provides a cost comparison.
So if you want a REALLY cheap building and don’t care when or if the post foundation will rot, you should build a post-frame building on a treated wood post foundation…
…or for roughly 10% more, you can build using Perma-Columns and have an investment that will hold its value for a very, very long time.”
Mike the Pole Barn Guru writes:
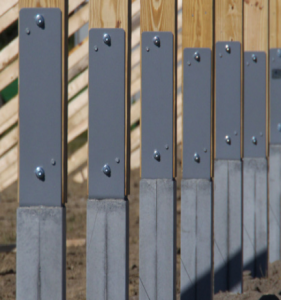
Perma-Column
This particular article has been triggered by a question posed by reader MATT in WABASH who writes:
“What is the cost of a perma-column? I am looking at a 40 x 56 building most likely at a residence that I will live long term and thought perma-columns would be a good investment, but I am having trouble finding the cost online for them. Thanks!”
Well Matt, as near as I can tell, the budget should be around $200 per column by the time they get delivered to your jobsite. Next challenge is going to be unloading and properly placing the several hundred pound Perma-columns exactly in the holes, on top of a poured concrete footing.
With the thought you are trying to avoid placing pressure preservative treated wood into the ground, there may be a more affordable (and easier to install) alternative. Assuming four foot deep two foot diameter holes, one could pour under one-half yard of premix in the hole and mount a bracket in it for roughly $100. Same longevity, same concept, easier to install.
$200, where did you pull that and the same amount for weight out of? I am no guru or expert myself but Midwest Permacolumn is the primary and premier creator and manufacturer of such columns to my knowledge, with Morton making a similar albeit their own design with added height adjustable metal base with no cost or way to purchase publicized like Mw Pc. The company’s lowest price is a little more than 100 coming in at 102.33 at 135 pounds up to 180.70 at 230 pounds for largest dimension of 8 size choices available for standard 5 foot column, with the 6 foot minus one size choice for lowest price of 149.34 and weight of 195 up to 243.95 at 343 pounds and tallest standard sizes also with 7 sizes to choose from at 154.87 at 226 up to 252.98 at 396 pounds. And they claim a 50 year life, again not much resistant to acid or ground chemical attacks leading to premature deterioration much like in a marine environment though longer life expectancy of at least 50 years with being resistant to “wood” boring insects though they can still climb or make a bride to get to food source above grade/ground. So I give you leniency to the 200 price and wight estimate as an out of the cloud ‘average’. And the link is an ‘authorized’ distributor thus the lack of prices and online ordering from what I could find on their web pages. Also Mw Pc makes and sell precast non-reinforced cookies. of the same concrete mix though they require a certified or licensed soil engineer to evaluate the site so as they can make a recommended sale for proper longevity for your foundation system. They also make a column for steel post/poles/uprights that are the heaviest at 975 pounds and priciest though no price is public, but still make for a more convenient foundation for faster erection and is 7 feet in height. They also do specialty concrete column foundations weighing in at 386 and much like the metal column foundation there is no price listed/shown but also same in height and from my best guess is for intermediary support which could also work for crawlspace raised floor support.
Thank you for this blog article though not sure when it was published/posted since I saw it under suggested related (random more like it ) links from another blog post.
I know somehow there is a point to your post Josh, I just don’t know what it is. The $200 is a budgetary figure and would include freight to get it to the jobsite and equipment for offloading.
Mike, the perma column puts a splice where the embedded column has the largest moment from wind loads.
The bolted connection makes a “hinge point” and thus reduces the strength of the column.
We have been approached by them and our evaluation is that for more money, you get less strength and less stiffness.
Duane Boice, PE
I agree with your analysis Duane!
Here’s your answer to all your problems!
Check out Concrete Pier System— We use these on our buildings and they are less expensive, and a lot easier to work with installation and labor.
Our crews love this system, and can jump from building to building! We don’t use any other system, and your building will last a lifetime! So there’s your answer – Concrete Pier System, has made an innovative & cost-effective system and the best way to build a superior building!!
One more thing, you don’t have to spend a ton of money shipping these to you- 50 on a pallet.. doesn’t break the bank.
Customer Service is great, and they help with shipping rates! – Right now (I think until the end of the year) they are doing 10% for contractors first order.
More contractors need to try these out for themselves! They will be impressed! – Karl – CR Contracting
Thank you for your contribution. We are currently researching this product as it does not appear to have ESR approvals for ICC. No approvals could limit use in jurisdictions requiring structural plan reviews.
Have you discovered additional information about engineering for the Concrete Pier System? From their website, they provide a structural engineer to contact but I don’t see a blanket approval to a particular standard. I want to build in Florida so must meet 2017 Florida Building Code which the Perma-Columns meet.
I have requested information repeatedly, to no avail. They do not have ICC ESR approvals, nor FBC approvals.
I was wanting a price
Thank you for your interest in a new Hansen Pole Building. One of our Building Designers will be reaching out to you shortly, or dial 1.866.200.9657 for immediate assistance.
According to the page on Facebook, I see that John at Heartland Perma-Column sold the business. Is there an archived site for all of his past articles?
Are you working with any other builder who uses Perma-Column? I know Graber in Indiana uses them.
I am unaware of an archived site for his articles. We have had several clients acquire their own Perma-Columns and our engineers have designed for their use.
Have you all ever herd of the base shoe and or base shoe and base shoe plates? Also Simpson makes a few versions of a bracket /Steel for making a connection of wood columns to concrete slab very strong connection reasonably priced. I can say this much about the Simpson product I was a part of a project and the architect that was involved in the project was also purchasing a space in this building when it was completed very high profile building downtown on main street 3,000,000+ I was the superintendent so with that said sounds like it might be Something you guys might at least take a peek at but they were also base shoes and bass shoe plates. That are designed and custom-made by your steel provider and designed by the architect and engineer from what I understand I’ve worked with both several different kinds but again I just know we’re supposed in thought I would share this information.
Simpson does not manufacture a column bracket capable of resisting moment (bending) forces, so they would not be an option. Base shoe plates appear to be more effort than would be required, when there are available ICC ESR approved wet set brackets readily available and relatively affordable.
A pole barn is a AG building. Using it for anything else, like a insulated shop or worse yet house, is a waste of time and resources. A insulated shop or house deserves stick built on a stem wall and will save man hours.
Having built and owned fully engineered post frame shop houses of my own for over 25 years, I disagree 100%. Post frame is less expensive, quicker to build, easier to super insulate – altogether a far better value than stick built on a stem wall.