Beyond Code: Preventing Floor Vibration
by Frank Woeste, P. E., and Dan Dolan, P. E
Floor vibration, or bounce, is not a safety issue — it’s a performance issue, and one that’s likely to be impor- tant to homeowners. No one likes to hear the china rattling in the cabinet when they walk across the room. But at what point is the floor stiff enough, and how can a builder predict how the floor will perform?
Unfortunately, there’s no clear-cut rule for a builder to follow, and the physics of vibration are so complicated that it’s no easy matter to design a guar-anteed bounce-free floor (see “Sizing Stiff Floor Girders,” Practical Engineering, 8/97). Also, “acceptable” floor perfor- mance is highly subjective: What’s good enough for one homeowner may not be good enough for another.
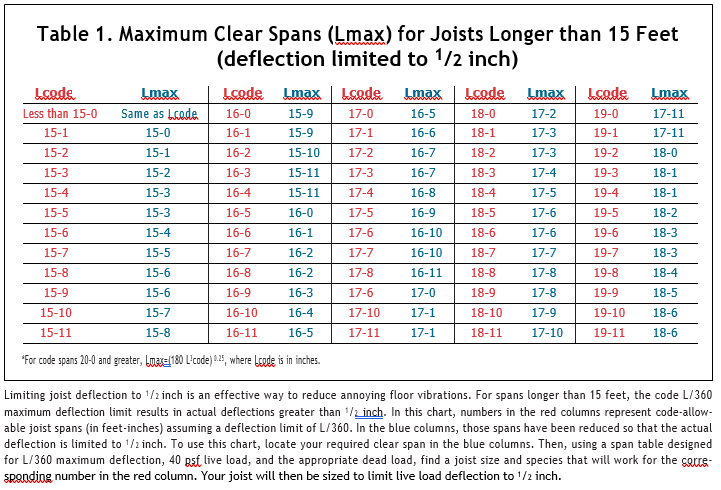
The building codes don’t help much in this regard. They’re primarily con- cerned with safety — in other words, the strength of the beam rather than its stiff- ness. The most stringent code limit for joist deflection is 1/360 of the span: For example, a joist with a clear span of 15 feet must not deflect more than 1/2 inch under live load (people and furniture). The dead load — the weight of the floor materials — is not typically included in calculating deflection.
And yet it has been known for decades that a span/360 live-load deflection limit will not necessarily yield floors that are acceptable to everyone when it comes to vibration.
The purpose of this article is to pro- vide some simple rules of thumb for tak-ing the annoying vibrations out of floor systems, whether you’re framing with solid-sawn joists, metal-plate-connected floor trusses, or wood I-joists. There’s no guarantee that every customer will be satisfied if you follow these guidelines, but they should prevent the vast major-ity of complaints.
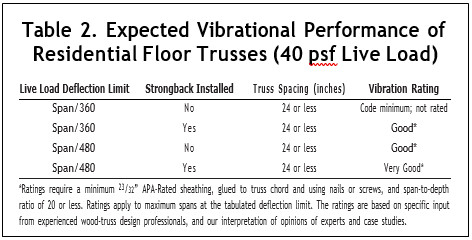
Some Quick Rules of Thumb
Before looking at specific types of joists, here are some general guidelines for controlling bounce.
✔Shorten the span. In general, shorter spans make for stiffer floors. For exam- ple, if the L/360 span table tells you a joist of a given size, grade, and species will just barely work for your span, shorten the span by adding a girder near the center of the original span. The resulting floor will vibrate less.
✔Increase the joist depth one size. If the code requires a 2×8 at 16 inches on- center, then use a 2×10 of the same grade and species. Or use a 14-inch- deep floor truss when a 12-inch deep truss would meet code requirements. This may not be the most cost-effective solution in every case, but it’s easy to remember and will save time and worry.
Probably the least efficient way to improve floor performance is to reduce the on-center spacing — 16 inches to 12 inches, for instance. Occupants feel “bounce” as a result of a foot impacting an individual joist. But even at 12 inches on-center, the joists are not close enough for the shock of a foot to be car- ried by two joists.
✔Glue and screw the sheathing. Floor sheathing should always be glued down. Screws work better than nails for long- term bounce control.
Design for Solid-Sawn Joists
Our recommendation for stiffening solid-sawn floors is a simple modifica- tion of a rule that was published in 1964 by the FHA: For floors up to 15 feet, limit live-load deflection to span/360; for spans over 15 feet, limit the live-load deflection to 1/2 inch (see Table 1, page 69). In adopting this rule, we encourage builders and designers to ignore the reduced live load of 30 psf for sleeping areas, and instead use the standard 40 psf live load for all rooms. After all, a bedroom can become a study or home office, and the traffic may be heavier than in a living room.
Metal-Plate-Connected Floor Trusses
Floor trusses are a unique product in that they accommodate effective strong- back bracing (see On the House, 7/98, for more on strongbacks). The consensus among wood truss professionals is that strongbacks are effective in minimizing annoying vibrations, and that they are well worth the time and money it takes to install them.
Table 2 illustrates the expected perfor- mance of various floor truss designs, using a 40-psf live load. Table 3 gives guidelines for sizing and installing strongbacks. For best performance, strongbacks should be installed near the center of the span (versus two at the third points) in upright position and attached to a vertical web. The strong- back should also be located at the bot-tom of a vertical web. To be effective, the strongback must be snugly attached to each web, as indicated by the nailing recommendations in Table 3.
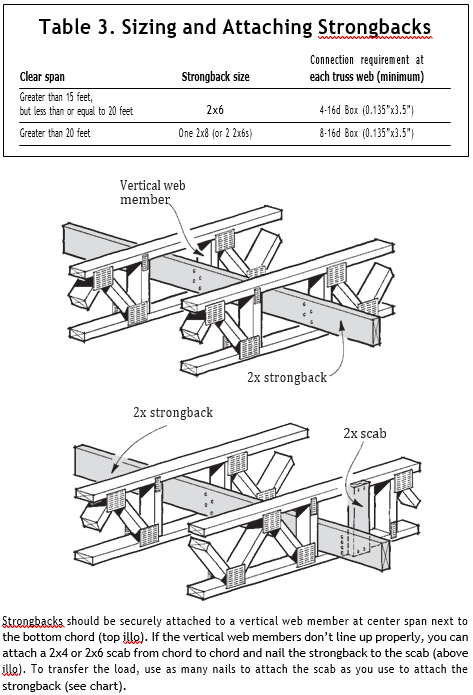
When, for whatever reason, the verti-cal webs don’t line up, you can attach a 2×4 or 2×6 scab to the top and bottom chords for attaching the strongback to the truss (see illustration). The total number of nails used to attach the scabs to the truss chords should match the number used to attach the strongback to the vertical web.
Some of the truss professionals that we interviewed when developing Table
2 had more restrictive rules to offer, but none had less restrictive design advice. Again, no design criteria is guaranteed to totally eliminate vibra- tions, but we believe that following the recommendations in the table will minimize complaints.
Wood I-Joists
When using wood I-joists, a simple way to get good results is to always use the tables designed for span/480 deflec- tion. Any I-joist stamped under the new APA standard for performance rated I-joists is automatically designed to meet the span/480 limit. The stan- dard also uses 40 psf as the minimum live load for any floor. The APA stan- dard is now being used by some I-joist manufacturers to make selection of I- joists easier. The allowable spans for various spacings are printed right on each joist.
Another design system for control vibration in wood I-joist floors is Trus Joist MacMillan’s TJ-Beam software. Trus Joist has done extensive testing of floor performance and has developed its own rating system. Using the software, a user can select a number between 20 and 70, with 70 offering the greatest level of protection against potential floor prob- lems as judged by an occupant. For example, a design that is rated at 55 is expected to be judged as “Good to Excellent” by 96% of the population, while 2% should judge such floors as “Marginal,” and 2% should judge the floor to be “Unacceptable.” This system allows the homeowners, through their contractors or architects, to select the level of floor performance to meet their expectations.
We tested the software for a 16-foot clear span supported by 2×4 walls (16 ft. 7 in. outside-to-outside), with I-joists 16 inches on-center and a residential load of 40/12 (live load/dead load). Using a 9.5-inch TJI Pro-250, the rating was 35. Increasing the depth to a 14-inch TJI Pro-250, the rating was a 53. Tightening up the spacing of the 9.5-inch I-joist to 12 inches on-center increased the rating only to 42 — illustrating that going to a deeper joist at the same spacing is a bet- ter solution.
The TJ-Beam software also provides a relative cost index that tells the user how much extra an improved floor will cost. Often an improved performance design can be obtained with the same or even lower cost than the original design.