This week readers “ask the Guru” about the use of hurricane straps on flat purlins, installing sheetrock to metal girts, and a question about specific lumber for a home build.
DEAR POLE BARN GURU: I am assembling my pole barn it is 20×28 with 8×8 purlins 16″ OC mounted on top of rafters sideways. Is there any issues with adding hurricane straps to better secure the purlins to the rafters? It is being built in a high wind area. Thanks, JOSH in APPLETON
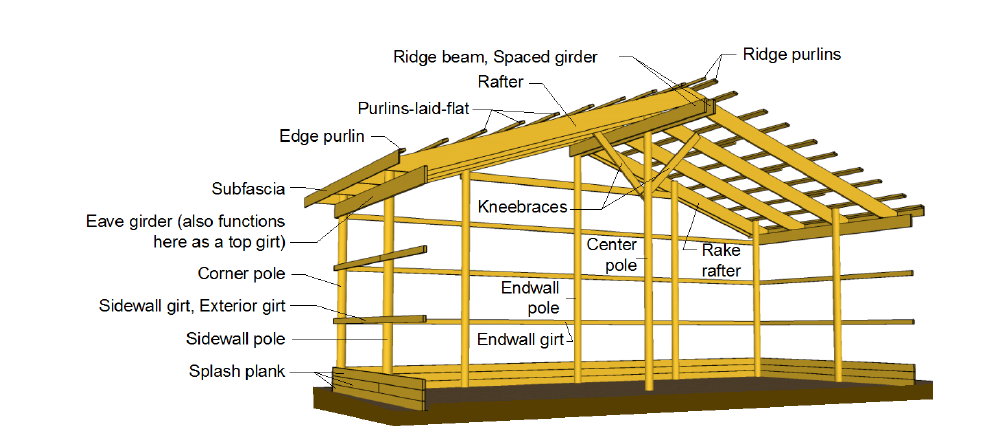
NFBA Design Manual Second Addition
DEAR JOSH: While adding hurricane straps will not hurt anything, they may not be adequate to resist uplift loads. Purlins on top of rafters do require solid blocking between (on top of rafter) to prevent rotation, as well. You should reach out to engineer who sealed your building’s structural plans for recommendations.
DEAR POLE BARN GURU: What would I need to do to hang sheetrock on the metal girts? Do windows need to be added in between the girts or can they be cut and framed for windows? Thanks! JORDAN in GARWIN
DEAR JORDAN: Provided metal girts are properly detailed to limit deflection and are no more than 24 inches on center, you can attach sheetrock with 1-1/2″ long fine thread drywall screws. You should never cut a girt, without it being shown on your engineer sealed plans, or reach out to your engineer directly for approval (and get a written confirmation). Adding openings to walls can compromise shear integrity of your wall and should always be done after, and only with, engineer’s approval.
DEAR POLE BARN GURU: Hello, We are designing a pole barn for our home. Our builder is using #1 kiln dried treated lumber and 6×6 posts every 10′, 3′ in the ground with post protectors. Questions: 1. Is this sufficient for a home? 2. Questions we should ask related to structural integrity? PS- the info you provide on your website is so helpful. Thank you very much!! KIM & JEFF in LAKE CHARLES
DEAR KIM & JEFF: Thank you very much for your kind words. Question #1 Depending upon your home’s footprint and height, as well as design wind speed and Exposure, these may or may not be adequate. Solid sawn posts (6×6) are generally an archaic design solution, as glulaminated columns are far superior in strength and performance. Question #2 Require your home to be constructed from fully engineered, site specific plans with verifying calculations. If it does not match up to Hansen Pole Buildings’ standards, something may be lacking. When it comes to YOUR building, will anything less than America’s STRONGEST design solution suffice?
Hansen Pole Buildings has provided hundreds of fully engineered, custom designed post frame buildings and barndominiums to our clients in Louisiana. Order direct 1.866.200.9657 and hire an erector or DIY and save tens of thousands of dollars https://www.hansenpolebuildings.com/2024/04/things-hansen-pole-buildings-does-better-than-any-other-post-frame-building-provider/