Site Storage Guidance for Long-Span Trusses
Originally published by: Construction Magazine Network(link is external) — February 3, 2021
The following article was produced and published by the source linked to above, who is solely responsible for its content. The Pole Barn Guru blog is publishing this story to raise awareness of information publicly available online and does not verify the accuracy of the author’s claims. As a consequence, The Pole Barn Guru cannot vouch for the validity of any facts, claims or opinions made in the article.
Editor’s Note: The article below is the second in a ten-part SBCA series on long-span truss installation guidance specific to the post-frame industry, all of which will be published in Frame Building News.
By Sean Shields, With Contributions by Jim Vogt, P.E.
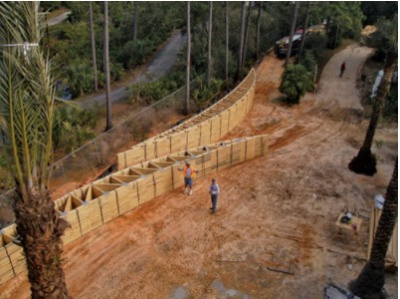
When handled and installed properly, metal plate-connected wood trusses are incredibly effective at spanning long distances while efficiently resisting intended design loads (gravity, snow, wind, etc.). The proper handling of trusses prior to their installation is very important, because significant damage may occur to wood members, plates, and joints when a truss bends out of plane—and this can affect their long-term performance (see Truss Techniques, Part 1(link is external) in the November 2020 issue of Frame Building News(link is external) for greater detail).
Correct installation is also vital. We’ll explore some best practices for common installation challenges in future installments of this series, but it’s important to address two additional topics prior to installation. One is long-span truss handling equipment, which we will tackle in the next article, and the other is truss storage on the job site.
Location, Location, Location
One of the most important factors in a successful truss installation, particularly in relation to long-span trusses, is choosing the most appropriate storage and staging location. Why? First, the location where the trusses are stored on the job site impacts the extent to which the trusses need to be handled. If you will be using a crane, the trusses should be stored and staged close enough to the building being erected that they only need to be lifted once, as they are set in place.
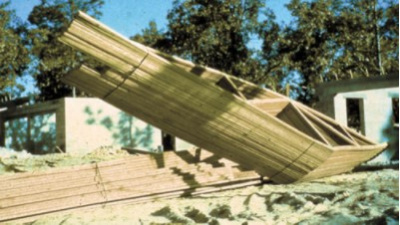
Requiring trusses to be double-picked (or hoisted twice) compounds the chances that the trusses may become damaged or installed out of order (or in the wrong orientation). The reason for this is because trusses are typically bundled in the order in which they are meant to be installed. Lifting and restacking bundles of trusses either reverses the intended order or requires the trusses to be scattered individually, increasing the opportunity for installation errors. Not to mention that double-picking will likely also increase the amount of time it takes to install the trusses, which in turn puts pressure on the framers to make up that time in other areas (often resulting in them pressing through other important aspects of the installation process).
If tele-handlers or other mobile equipment is used to move the trusses, the larger the distance between where the trusses are stored and staged and the new building, the more opportunities there are for damage as the equipment maneuvers over the rough terrain on the job site.
Prepare a Way
For these reasons, it is beneficial to choose a storage and staging location for the trusses early on in the site preparation process. While there may not always be a lot of flexibility or options when it comes to truss storage on the job site, it’s important to consider several factors when weighing the best possible location.
As the first section of this article points out, proximity to the installation area is likely the most important factor to prioritize. To the greatest extent possible, the trusses should also be placed in an area that does not obstruct normal traffic flow on the job site. Creating an obstacle on the job site increases the opportunity for other equipment and materials to come in contact with the trusses, potentially causing expensive damage.
Many times, long-span trusses need to be prepped prior to installation. Ensuring there is sufficient room around each truss to mark purlin locations on the top chords and/or affix T- and L-web reinforcement can speed up the process and make life a lot easier for everyone involved in the installation process.
SBCA’s Building Component Safety Information (BCSI) handbook states in the B1 section (www.sbcindustry.com/b1(link is external)): “Trusses may be unloaded directly on the ground at the time of delivery or stored temporarily in contact with the ground after delivery. If trusses are to be stored horizontally for more than one week, place blocking of sufficient height beneath the stack of trusses on 8′ to 10′ intervals (or as required) to minimize lateral bending and to lessen moisture gain from the ground.”
While the trusses can be stored directly on the ground, minimizing lateral bending is key. This means that the site chosen for truss storage and staging needs to either be level, or blocking need to be placed on the ground ahead of time to create a level bearing area for the trusses while they are stored. Moisture gain also needs to be minimized. This means the storage area should be reasonably dry and preferably in an area that will not collect water in the event of a rainstorm.
The B1 section further states: “Trusses stored for more than one week shall be protected from the environment in a manner that provides adequate ventilation of the trusses. If tarpaulins or other protective covers are used, the ends shall be left open for ventilation. Tight-fitting coverings are not recommended, since they can trap moisture.” Excessive dirt and/or moisture gain can impact both truss installation and long-term truss performance, so it is a best practice to protect trusses from both while they are stored on the job site.
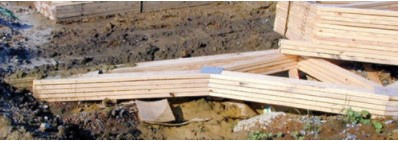
Communication Is Key
Of course, all the site preparation and planning done ahead of time goes to waste if it isn’t communicated effectively to the person delivering the trusses. In most cases, the individual delivering the trusses has never been to the job site before they show up. It may or may not be clear to them where traffic naturally flows throughout the job site. It may also be unclear where rainwater is most likely to collect, creating troublesome puddles and mud. They are also unlikely to know the equipment that will be used to handle trusses on the job site or the hoisting radius of the crane being used to set the trusses in place. Finally, they will not know how long the trusses will need to be stored prior to installation.
In short, it should not be left to the person delivering the trusses to choose where they should be stored and staged on the job site. The earlier in the process the truss storage site is chosen, the easier it is to not only flow the rest of the job site around it (e.g., not storing other building materials in the same location that will then need to be moved upon the truss delivery), but also communicate that location to the person delivering the trusses.
While a phone call ahead of delivery will likely suffice in some instances, there are several other best practices that can be employed to ensure there isn’t any confusion at the time of delivery. The easiest, when possible, is to take one or more photos of the job site and send them to the driver ahead of time. Outlining the area with a few stakes or marking spray paint on the ground can also ensure the trusses are placed as close as possible to the predetermined spot. A quick sketch of the job site, with the truss storage area clearly marked, can also be photographed and sent ahead of time.
The Bottom Line
A little forethought about the best location to store trusses on the job site can have a significant impact on not only how well their installation goes, but how well they perform over the long term. Having a solid storage plan is good. Communicating it effectively to the person delivering the trusses ahead of time makes the plan even better.