Providing Digitally Signed Structural Plans in Florida
Reader JEFF in TAMPA writes:
“Have an existing slab approx. 12×20 and slightly out of square on 7 acres of land. Want to erect a simple, square (approx. 13×21), hip-roofed (5/12 pitch) pole barn over the slab with two lean-to, open carports on either side (pictures of layout attached). Can you provide digitally signed plans for county permit authorities in Hillsborough county (must be signed by a P.E., architect or other professional licensed in Florida)? If yes, let me know the approximate cost. Thank you. Plan to use glulaminated pressure-treated lumber (12′) 3 ply 2×6 lumber for the 20 poles if I can them in Florida.”
Hansen Pole Buildings has provided thousands upon thousands of fully engineered post-frame buildings in all 50 states, including roughly a hundred to our clients across Florida.
Your layout pictures Jeff, sadly did not make it.
While full hipped roofs are lovely, they do not often lend themselves well to adding lean-tos, especially if the building has endwall overhangs (transition at hip corner to lean-to single slope becomes ‘messy’).. You may end up being best served by considering a 21 foot span gabled roof, all at the same eave height. Center portion could easily be enclosed with open carports at each end. This also provides for greater clear height under roof only areas.
We can certainly provide fully engineered plans, digitally signed by one of our experienced third-party Florida engineers and they will be included as part of your investment in your new Hansen Pole Building (and yes we can include true glu-laminated building columns). Our engineers will only seal plans when we are providing materials, as some of what they specify is proprietary to us and there is no way to guarantee an alternative supplier will actually deliver them.
Tag Archives: gable roof
This ended up being an interesting exercise and it yielded results pretty much as I had expected.
Reader RON in MONROE writes:
“Can you tell me the approximate percentage difference in pricing or cost of the different building styles? I know this will vary according to the size of the building, etc., so let’s pick a 38 by 38 by 17 foot tall building. How much more to move up from a single slope to gable style, to monitor, and to Gambrel?”
Mike the Pole Barn Guru responds:
There are so many variables involved in this question it is impossible to answer. And an answer for one given set of climactic loads (snow, design wind speed and exposure) would not translate to any different set of variables. Even as to where you are going to measure 17′ to is a huge impact. On a single slope – is this measure of low wall or high wall? Would it be clearspan or have interior columns? Is monitor measure to low side of wings, or raised center? If low side of wings, then how tall would center be? Gambrel, is your measure to eave side of steep slope or to pitch break? With a 17′ height, would there be an intention to have a full or partial second floor? Would this building be a garage/shop or a residence? It makes a difference as loading criteria are different and if drywall will be attached to walls or roof, a greater deflection stiffness is required. Even features such as overhangs can change your percentages as monitor style is going to have four eave sides.
If you are looking for cost effectiveness, footprint multiples of six feet are going to get you there (lumber comes in two foot multiples, steel roof and siding in three foot).
A gabled roof will be your least expensive and easiest to build, however not always aesthetically your best design solution. I recommend you determine what your finished space needs will be and discuss options with Rachel your Hansen Pole Buildings’ Designer.
RON wanted just a little bit more:
“Just use a peak height, no doors, no windows, same snow load, everything the same.”
Pole Barn Guru replies:
Drum roll …….
And the envelope please …….
Here are results:
I did have to change roof slope on the single slope to 2.84/12 in order to have an eight foot eave height on the low side.
Monitor was 5.6% more than gable, gambrel 10.4% more, single slope 17.6% more.
In an attempt to preserve “pristineness” of neighborhoods, Planning Departments can come up with some interesting requirements. Amongst these are often restrictions upon building heights. Sometimes restrictions for detached accessory buildings (garages or shops) are related to primary dwelling heights, sometimes they appear entirely arbitrary.
In the case of our “shouse” (shop/house) in South Dakota, there was a restriction on any building having a sidewall height of 10 feet. We solved this by erecting a gambrel with sidesheds, where sidewall steel lengths were just under 10 feet (although overall building height is 44 feet)!
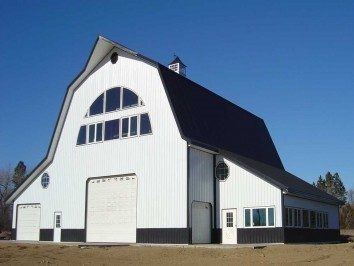
*Our “shouse” with 10′ sidewalls
Reader BILL writes:
“Good morning,
I have a customer who wants a pole barn for his RV. We have issues with height restriction. He wants a 10 x 14′ high garage door but we have a max height restriction of 14′ to the mid span of the roof. My question to you is this: can we get a building that can have say 10′ high side walls, a 10′ wide x 14′ high garage door on the end and meet the height requirement? Not sure if you can design a truss to accommodate this. It can be a gable roof, gambrel roof, or any other roof that will work. The side walls can be any height as long as the roof height meets the requirements (I only said 10′ as a guide).
They would like 30′ width but that may be too wide for the coverage. I was thinking 24′. They want it 60′ deep.”
Mike the Pole Barn Guru responds:
Provided they can stand 8 interior columns, you could go with a gambrel formed by using a 12′ x 60′ x 16’6″ center portion where overhead door would be placed. With a 4/12 slope your peak height would be 18’0″. On each side of center, place a 6′ x 60′ single sloping shed from 16’6″ to 10’0″ (13/12 slope). This will put average roof height at 14′ and will give an exterior gambrel appearance. If they want to go 30′ wide, make sheds 9′ wide and change steep slope to 8.67/12.
While this appears to sound like it is a circumvention of restrictions, it does meet with the “Letter of the Law”.
Faced with what feels to be an overwhelming challenge of height restriction vs. wants and needs? Please call 1(866)200-9657 and speak to a Hansen Pole Buildings’ Designer. Chances are good we can find options for you.
Ignorance is Bliss and Sometimes Architects are Happy
Portions of this article (in italics) are from “County explores options for new Highway building” April 29, 2019 by Nathan Bowe at www.dl-online.com
A city plow truck goes by the main shop building at the Becker County Highway Department complex in Detroit Lakes. www.dl-online.com File photo
Dear Architect friends ~ I didn’t learn much in architecture school, however one nugget was, “It is all about presentation”. Before you need to give a presentation including a possible post frame building, please discuss it with me, or at least read a few of my pertaining articles. I want you to come across as being as knowledgeable as possible.
“Hoping to save money on a new Becker County Highway Department facility, made of precast concrete and estimated to cost about $8 million, commissioners are exploring other types of buildings.
They are considering options including precast concrete, steel, and pole barn, and will tour facilities in the area made of those materials.
The firm working on the project, Oertel Architects of St. Paul, said in a report that any type of material could essentially be made to work, but a pole barn-type building would have to include steel in places to support a 5-ton crane in the maintenance area, for example.”
Post frame (pole barn) buildings can easily be designed to support a 5-ton crane: https://www.hansenpolebuildings.com/2013/07/overhead-crane/
“A less-expensive pole barn building also comes with a much shorter projected lifespan, and generally brings more problems with leaks and maintenance, unless a better grade of roof is used.”
Post frame buildings are permanent structures easily capable of generations of useful lifespan. Properly installed steel roofing will last decades without leaks or needs for maintenance.
“A pole barn is considered an agricultural type building in the industry, and is also referred to as timber frame. This is essentially like building a structure like an old-fashioned barn, with large timber columns and frames. It is typically made without a perimeter foundation. The wood frame structure is typically covered with a metal skin and the low-gable roof type is typically of metal. Its lifespan is projected at 15-30 years, depending on maintenance and other factors.”
Post frame and timber frame buildings are totally different animals. Post frame buildings have been used commercially longer than I have been in this industry (nearly 40 years). Very few buildings provided by Hansen Pole Buildings would be termed as being purely agricultural – nearly all are residential or commercial. Isolated columns embedded below frost depth preclude needs for expensive and inefficient continuous concrete foundations. (Check out foundation costs here: https://www.hansenpolebuildings.com/2011/10/buildings-why-not-stick-frame-construction/). Most typically post frame buildings have 4/12 roof slopes (rather than “low” as in all steel buildings).
Amazingly, it appears my now 15 year-old million-dollar post frame home is due to expire any time now (like Windows 7)! In reality a properly engineer designed and constructed post frame building will outlive any of us who are reading this article.
“One way to meet the highway department needs and still meet code using pole barn construction would be to build three or four separate buildings, or build one building at different heights for vehicle maintenance, vehicle washing/storage, and office space, Oertel reported.”
Post frame buildings can be easily designed with a multitude of different wall/ceiling heights.
“Pole barns tend to be less energy efficient over time.”
As post frame buildings use exact same insulations as other similar construction types, if this is true it would be applicable across all construction spectrums. Post frame lends itself well to creation of deep insulation cavities and is far easier to insulate than all steel or precast concrete.
“Structural steel works better in a public works facility, with more salt and moisture in the air than usual, since these are made of heavy steel, just like a steel bridge. It is the less substantive metal materials that are a concern. A pole barn uses thin steel gusset plates and there is not much material to last over time if corrosion is present. Metal panels commonly used in pole barn buildings are also easily marred or dented by heavy duty operations.”
In highly corrosive atmospheres, steel can be isolated from corrosion (as in galvanized steel “gusset plates” used to connect roof truss members). Any type of siding – or even precast concrete or masonry, can be damaged by careless operations. Use of strategically placed bollards (https://www.hansenpolebuildings.com/2017/05/lifesaving-bollard/) can eliminate possibilities of significant damages.
“However it’s constructed, the new public works building will need the same mechanical, plumbing and electrical systems, floor loading, earthwork and mechanical systems, Oertel said. Costs can vary, but all of that might add up to perhaps 60 percent of construction costs, with the actual building structural shell 20 to 25 percent of the total project cost. So cost savings from a cheaper type of building might not be all that commissioners might hope for, compared to the long-term drawbacks.
“More could be said about the differences between pole barn construction and a more heavy duty construction using precast concrete,” the report sums up. “It mostly comes down to a lower front-end cost with a pole barn, at the sacrifice of longevity…””
Post frame construction is going to provide a greater value, without being “cheap”. Post frame buildings will have a usable lifespan as great as any other permanent building.
And – have you ever tried to remodel a precast concrete building?
Can I replace Gable with Gambrel Trusses?
Welcome to our newest feature: Ask the Pole Barn Guru – where you can ask questions about building topics, with answers posted on Mondays. With many questions to answer, please be patient to watch for yours to come up on a future Monday segment.
Email all questions to: PoleBarnGuru@HansenPoleBuildings.com
DEAR POLE BARN GURU: Hi, I have a morton pole building with a regular pitch roof on it and was wondering if it would be possible to take off my trusses and put Gambrel trusses back on it? Also would that even be cost effective? could I resell the other trusses? Does your company do that type of work? Thanks,Rick
DEAR RICK: While nearly anything is possible, the practicality and cost would probably deem this to be a project you would not want to tackle. This is more than just replacing the roof trusses. If you are considering the gambrel trusses as part of a system with an inhabitable attic space, the footings beneath the columns will not have an adequate diameter to support the load. This puts the project in the realm of complete disassembly and reassembly. If your existing building is more than just a couple of years old, the existing trusses would not be resalable, as the Building Codes have changed, causing a different interpretation of how snow loads are applied to roofs.
Your best bet, if you want a gambrel style roof, is to construct another building with gambrel trusses.
DEAR POLE BARN GURU: Hi, I am considering building a pole building house. My concern is the life of the poles. Will the poles rot after time when in the ground? They would need to last a lifetime. Or would studs placed on a slab be better instead of the poles? Thanks for your help. WONDERING
DEAR WONDERING: There is no reason to believe a properly treated column (pressure treated column to UC4B) will not last far longer than either of us will be around to see. I have two very nice pole buildings at home – one is now 22 years old, the other 18. Both are multiple stories, insulated, drywalled, etc. I expect both of them to outlive my grandchildren. I would not have invested the money into them that I did, if I did not expect them to be forever buildings. We have sold buildings for years used as pole building houses, and have yet to have anyone say their poles were “rotting off”.
Click on a couple of the links below for more information. Email us for a Product Guide, and you will see pictures of everything from houses to commercial buildings…all pole buildings.
For more information on the Building Code standards for properly pressure treated columns: https://www.hansenpolebuildings.com/blog/2012/10/pressure-treated-posts-2/
As to why not stick frame: https://www.hansenpolebuildings.com/blog/2011/10/buildings-why-not-stick-frame-construction/
DEAR POLE BARN GURU: Hello, Can you please tell me how one would describe the difference between a portable barn and a permanent barn? I believe that a barn is portable when made from panels that clip together and have no part cemented to the ground. A portable barn would be attached by clips to corner poles cemented into holes. By removing the clips, once could then disassemble the barn, right? Is that what makes it portable? I am writing because if I put up a barn as part of my business I want to be able to move it easily if I should move.
Thanks, PORTABLE PAULA
DEAR PORTABLE: To me, if it is portable I can back a truck up to it, hook the hitch onto the ball on the back of the truck and drive away with it because it has an axle and wheels.
Every permit issuing jurisdiction is going to have their own definitions of portable and permanent, as well as requirements for permits, foundations, etc. A building with panels which clip together, may be classified as being temporary, rather than portable and there may be a limited time frame for you to be able to use it such as 90 or 180 days, before it must be taken down.
You really need to go visit your local planning department, who can give you definitive answers based upon where you propose to use the building. What may be allowable in one jurisdiction may be not only a “no-no” in another, but also subject to fines. Unless I know exactly where you are, and specifically where you propose to put the building, I am limited somewhat limited in what I can advise.
Nothing is worse than a roof gone wrong. Leaks frustrate everyone involved, and are usually avoidable. Poor design and poor installation are equal factors in the roofs which just are not happy.
Avoid Valleys
Designing the roof of a pole barn? Then try to design a roof without any valleys. Valleys concentrate water and often clog with ice. It’s far more common to have leaks or ice dam problems near valleys than in the middle of a simple gabled roof. Many valleys exist because of a designer’s conceit rather than necessity. Often, these valleys trace back to the mistaken belief a chopped-up, complicated, multi-plane roof looks better than a simple gable. It doesn’t. And more complicated roofs are more expensive.
Just say no to Dormers and Skylights
No good reason exists for a new pole building to have a dormer. When I see a dormer, I conclude the designer or the architect made a mistake. They didn’t include enough interior space, and the building owner was forced to cut a hole in the roof because the ceiling was too low to stand up. Want to build a multi-story pole building – no problem. Want two floors, build two floors. Want three floors, build three floors. Then build a roof over the top floor. This roof should not have any deliberate holes in it. The “no holes” rule covers both dormers and skylights. Skylights are an invitation to leak – no matter how great the flashing kit is, pretty well plan upon them leaking, if they don’t it is a surprise bonus.
In most cases Single Slope Roofs are not less expensive
They also create a very tall wall on one side of the building, which has to be engineered for. Lots of “dead air” space ends up being paid for. There is not a ridge which can be easily vented. Worst of all – most people find them aesthetically unattractive.
An Unconditioned Vented Attic is better than an Insulated Roof
It makes more sense to put insulation on a flat ceiling than to try to insulate a sloped roof, for several reasons. Purlins usually aren’t deep enough to hold a thick layer of insulation; on the other hand, it’s usually easy to add a deep layer of insulation to the attic floor. Insulating the attic floor is also cheaper. Leave the space between purlins uninsulated, it will be easier to locate roof leaks. It is easier to air seal a flat ceiling, rather than a vaulted ceiling. If roof sheathing is used, damp roof sheathing will dry out quicker if it faces an attic than if it is part of a cathedral ceiling.
The Best Roof Shape is a simple Gable Roof
In a cold climate, the ideal design is a simple gable. Since gables don’t have any valleys or hips, they are easy to vent. It’s a straight shot from the soffits to the ridge. Chopped-up roofs with a variety of intersecting planes are hard to frame, hard to keep watertight, and hard to vent. Every nook and cranny creates somewhere for tree needles and ice to accumulate.
In a hot climate, a hipped roof can make more sense than a gable, because a hipped roof makes it easier to provide shade on all four sides of the pole barn. In a hot climate, shade is good. Fortunately, people in hot climates rarely have to worry about ice dams.
In all climates, make overhangs generous. If building a gable roof, don’t forget the rake overhangs; most rake overhangs are too stingy. Frame the rake overhang with overhanging purlins.
Don’t reduce the Roof Slope between the Ridge and the Eave
A good roof plane has a consistent slope from the ridge to the eave. A roof which changes slope at midpoint is disturbing. Especially disturbing is a steep roof which suddenly switches to a shallow pitch (for example, when a porch with a shallow-pitched roof is affixed to a pole building with a steep roof). Shallow slopes hold snow and are susceptible to leaks. Most steel roofing warranties are void on slopes of less than 3/12.
Make sense so far? Come back Monday when I finish up on my recommendations for making your roof affordable, long lasting, and pleasing to the eye.